Preparation of PDMS Stamps
(PDMS – POLY DIMETHYLSILOXANE)
An elastomeric stamp is the key element of soft lithography. It is usually prepared by replica molding, by casting the liquid pre-polymer of an elastomer over a master that has patterned relief structures on its surface.
Why use PDMS?
It is the unique surface behavior of PDMS that allows for most of the applications. The surface energy is a manifestation of intermolecular forces. The organic portion in PDMS is the methyl group, which has almost the weakest intermolecular forces. The inorganic siloxane backbone, one of the most flexible polymer backbones, allows the methyl groups to be arranged such that PDMS has almost the lowest surface energies known (expensive fluorocarbon polymers have the least surface energy).
Materials:
Sylgard 184 elastomer (consists of pre-polymer and curing agent)
Dessicator
Oven capable of reaching 70°C
Master that has patterned relief structures (CD/DVD)
Plastic cup
Plastic fork
Sharp scalpel
Petri dish
In a plastic cup, weigh 10 parts (by weight, ~ 20 g) of Sylgard 184 pre-polymer and 1 part (~ 2g) of curing agent.
Mix the above vigorously for a couple of minutes until the entire mixture is filled with bubbles.
Place the cup in a desiccator to degas (allow bubbles to rise out) for 20 minutes.
Pour the mixture slowly into a petri dish that contains the prepatterned structure (DVD/CD). Avoid bubbles and make sure that the master is lying flat on the bottom of the petri dish. The mixture should cover the CD/ DVD masters completely. The PDMS layer should be about 2mm thick (you may not use all of the polymer).
Place the petri dish in an oven and cure it at 70°C for an hour.
Using a sharp scalpel, evenly and gently cut around the pattern.
Remove the stamp using a pair of tweezers. This video depicts a small stamp being cut from the much larger polycarbonate master of the CD.
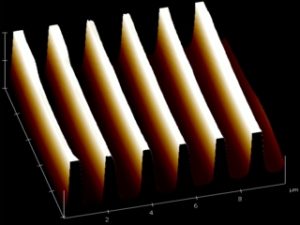
Stamp cut from the much larger polycarbonate master of the CD
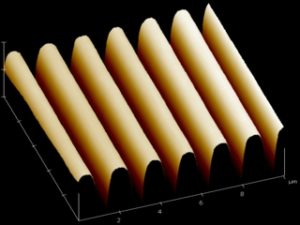
Stamp cut from the Al master